Quy trình sản xuất đặc biệt
Nhờ không ngừng theo đuổi các quy trình cải tiến liên tục và sản xuất tinh gọn, Toyota Motor Corp. trở thành nhà sản xuất ô tô lớn nhất thế giới trong đó có quá trình mang tên Monozukuri.
Monozukuri là từ ghép tiếng Nhật, trong đó "mono" là sản phẩm và "zukuri" là quá trình tạo ra sản phẩm. Monozukuri là đặc trưng của tinh thần Nhật, đòi hỏi tạo ra những sản phẩm có chất lượng cao, đáp ứng yêu cầu của khách hàng với niềm tự hào tiêu chuẩn Nhật.
Nhờ hệ tiêu chí này, Monozukuri đã được ứng dụng rất thành công trong các doanh nghiệp Nhật Bản, mà tiêu biểu là thương hiệu Toyota.
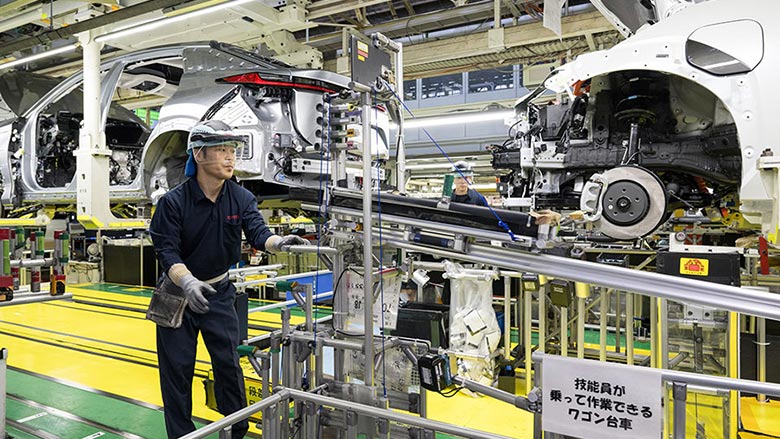
Kĩ sư làm việc tại Toyota.
Công ty này đã tạo ra một môi trường làm việc chuyên nghiệp, thúc đẩy tính sáng tạo và nỗ lực của con người. Mục tiêu của Toyota hướng đến chuẩn hóa năng lực nhân viên, tối ưu hóa quy trình sản xuất và cải tiến không ngừng.
Toyota hiện đang triển khai nhiều kế hoạch triển khai các kỹ thuật mới, chẳng hạn như mô-đun giga-cast, dây chuyền lắp ráp tự hành và công nghệ bản sao kỹ thuật số, để duy trì tính cạnh tranh trong ngành công nghiệp ô tô đang phát triển nhanh chóng.
Quy trình sản xuất lấy con người làm trung tâm
Trong xu hướng công nghệ ngày càng phát triển, tập đoàn này tiếp tục đổi mới, xây dựng các kế hoạch triển khai hoạt động sản xuất lấy con người làm trung tâm từ đó đẩy nhanh hiệu quả sản xuất và nâng cao an toàn phương tiện.
Ông Lando Nishida, Giám đốc điều hành cấp cao của Honsha Associates cho biết: "Một trong những khía cạnh đáng chú ý nhất trong cách tiếp cận của Toyota là sự tương tác liền mạch giữa con người và robot trong lĩnh vực tự động hóa. Sự cân bằng giữa chuyên môn của con người và đổi mới công nghệ thực sự độc đáo".
Ông Nishida chỉ ra rằng: "Tại các nhà máy của Toyota, người vận hành không chỉ giám sát robot; họ tích cực tham gia vào việc đào tạo họ, thúc đẩy văn hóa cải tiến liên tục cho cả con người và máy móc".
Xe điện thế hệ tiếp theo của Toyota sẽ được xây dựng dựa trên cấu trúc mô-đun mới, trong đó thân xe được chia thành ba phần: phía trước, giữa và phía sau. Phần trung tâm sẽ chứa pin thể rắn, có khả năng sạc nhanh hơn và phạm vi hoạt động dài hơn so với pin thông thường.
Cấu trúc mô-đun mới đòi hỏi phải chia gầm xe, bao gồm khung phía trước và sàn cabin, thành ba phần, mỗi phần được trang bị các bộ phận riêng.
Quá trình bắt đầu bằng việc bơm hợp kim nhôm nóng chảy vào khuôn ở tốc độ và áp suất cao. Chỉ trong vài giây, vật liệu được làm nguội từ 700C đến 250C và đông đặc lại, sau đó khuôn được mở ra để loại bỏ chi tiết đúc tích hợp.
Quá trình trên tích hợp kỹ thuật mới "gigacasting" (công nghệ đúc nhôm kích thước lớn), giúp Toyota chuyển từ việc sử dụng nhiều bộ phận và quy trình ép lạc hậu sang việc sử dụng ít bộ phận hơn, giảm chi phí và trọng lượng.
Nhằm tích hợp công nghệ mới một cách tối đa, các kỹ sư của Toyota đã tập trung vào việc cải thiện năng suất bằng cách giảm hai loại lãng phí: thời gian phải ngừng hoạt động để thay khuôn và quá trình sản xuất lỗi hoặc làm lại.
Toyota cũng phát triển "dây chuyền lắp ráp tự lái" để tăng tính linh hoạt trong nhà máy và sử dụng công nghệ bản sao kỹ thuật số để cải thiện quy trình sản xuất.
Các kỹ sư của Toyota cũng đang sử dụng công nghệ bản sao kỹ thuật số để thiết kế quy trình sản xuất hai chiều nhằm tăng năng suất và hiệu quả. Mục tiêu là cải thiện nhà máy và thiết bị thông qua các cải tiến được nâng cao về mặt kỹ thuật.
Bình luận bài viết (0)
Gửi bình luận